The essence of our sustainability commitment, which we summarise as “Performance up. Footprint down”, is to quickly transition to a low-carbon, circular economy with drop-in sustainable styrenics solutions for all applications that are on par with conventional product performance. We are investing to deliver on our vision and have a clear line of sight on the complexities and regulatory factors that will determine our success. Read on to find out how we plan to deliver on this promise.
With “Performance up. Footprint down.”, we address two mounting challenges for our industry: the prevention of littering and waste, and the reduction of carbon emissions.
This has been crystallised into three sustainability goals for INEOS Styrolution: save one million tonnes of CO2e* in 2030; sell half a million tonnes of INEOS Styrolution ECO products in 2030; and guarantee 100% regulatory compliance for both our conventional and ECO products. Our ultimate objective is to transform to a net-zero emissions business by 2050.
Our commitment to sustainability
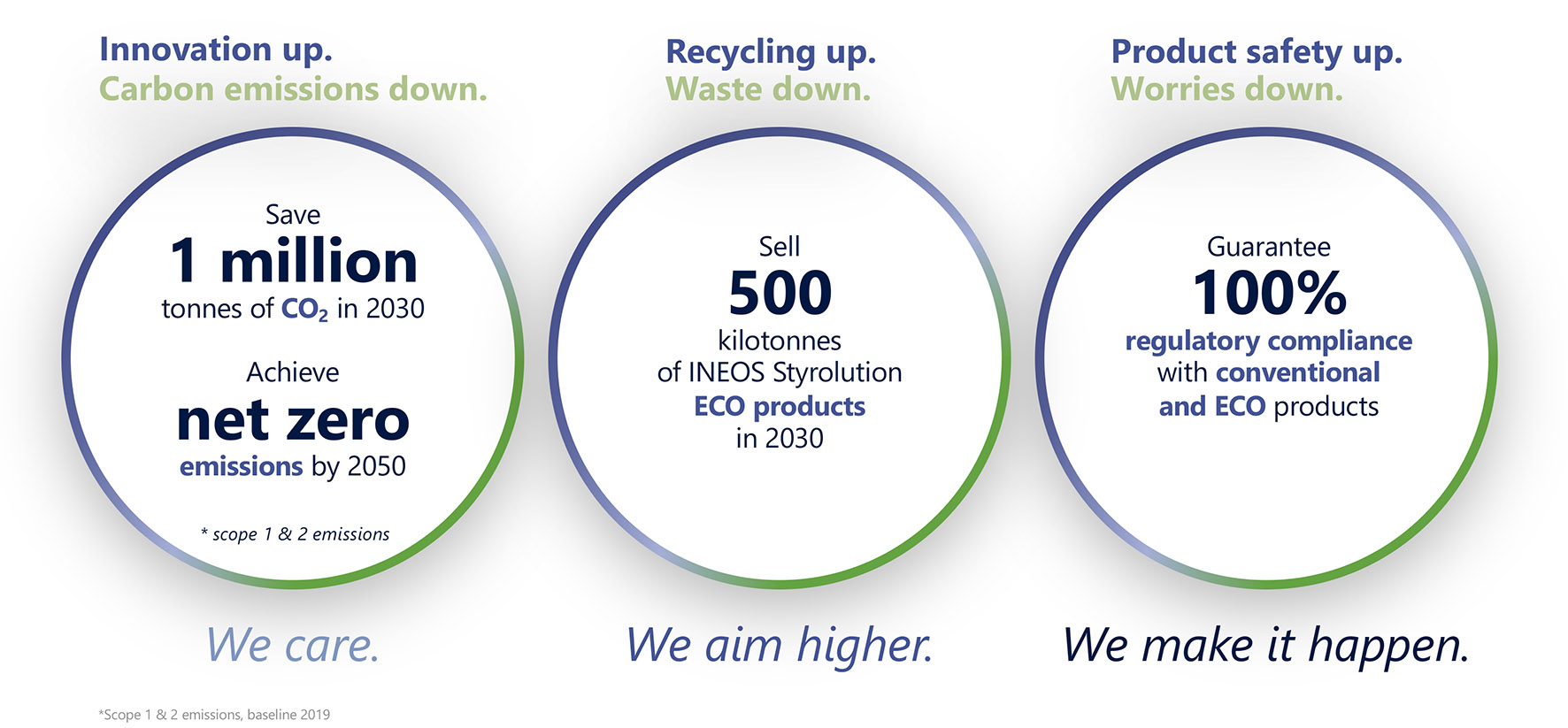
We have already made significant progress by scaling up our ECO portfolio and developing a tangible emissions reduction roadmap. Our broad portfolio of ECO products is our drop-in solution for customers, which means that ECO products can be produced using existing machinery and equipment with no additional technology or investments.
* CO2e refers to carbon dioxide equivalent (for our scope 1 & 2 emissions with 2019 as baseline)
INNOVATION UP. CARBON EMISSIONS DOWN.
We have developed a strategic roadmap to reduce CO2 emissions, and are already implementing four of these clusters today.
Our path to a low-carbon economy
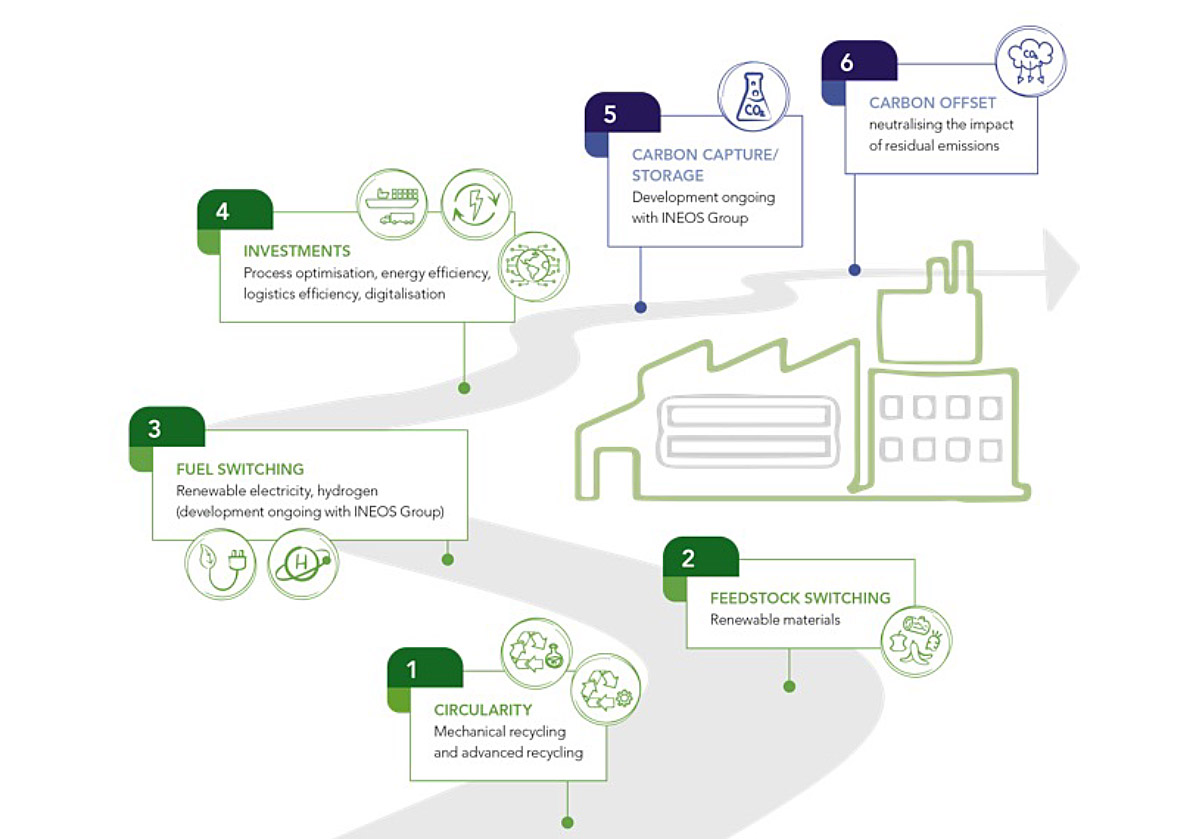
We start with switching our feedstock from hydrocarbon-based fossil to more circular and renewable materials. By becoming more circular, we aim to close the loop at the end-of-life phase of our products. Therefore, we are investing in mechanical and advanced recycling of our polystyrene and ABS products, which we believe will significantly reduce carbon emissions, reduce waste, and keep valuable materials in use for longer life cycles. We can also integrate renewable feedstock that complies with the sustainability criteria set by the International Sustainability and Carbon Certification (ISCC). In other words, feedstock switching. Both of these options offer a lower carbon footprint than conventional solutions.
The third cluster is fuel switching or the switch to green energy. This amounts to approximately one third of the CO2 emissions we want to reduce by 2030. And then number four, the biggest cluster, is process optimisations and investments in our sites to bring energy efficiency up and carbon emissions down.
We have committed to spend up to €1 billion euros by the year 2030 to advance these technologies. Longer-term, we will also look at other options such as carbon capture, storage and utilisation or carbon offsetting if required.
To date, we have saved 10% of greenhouse gas emissions compared to our 2019 baseline, primarily through investments in our sites and strategic switches to clean energy. This will bring us to the important milestone of 1 million tonnes of CO2 reduction in 2030, corresponding to 45% of our total GHG emissions. Reaching our goal of net-zero emissions by the year 2050 will require a full portfolio of further reduction measures, which we are actively working to identify.
RECYCLING UP. WASTE DOWN.
The one unique strength of our styrenics products, and in particular polystyrene (PS), is that compared to other polymers, we can apply every major recycling technology to styrenics.
Recycling technologies and renewable feedstock as pathways to circularity for styrenics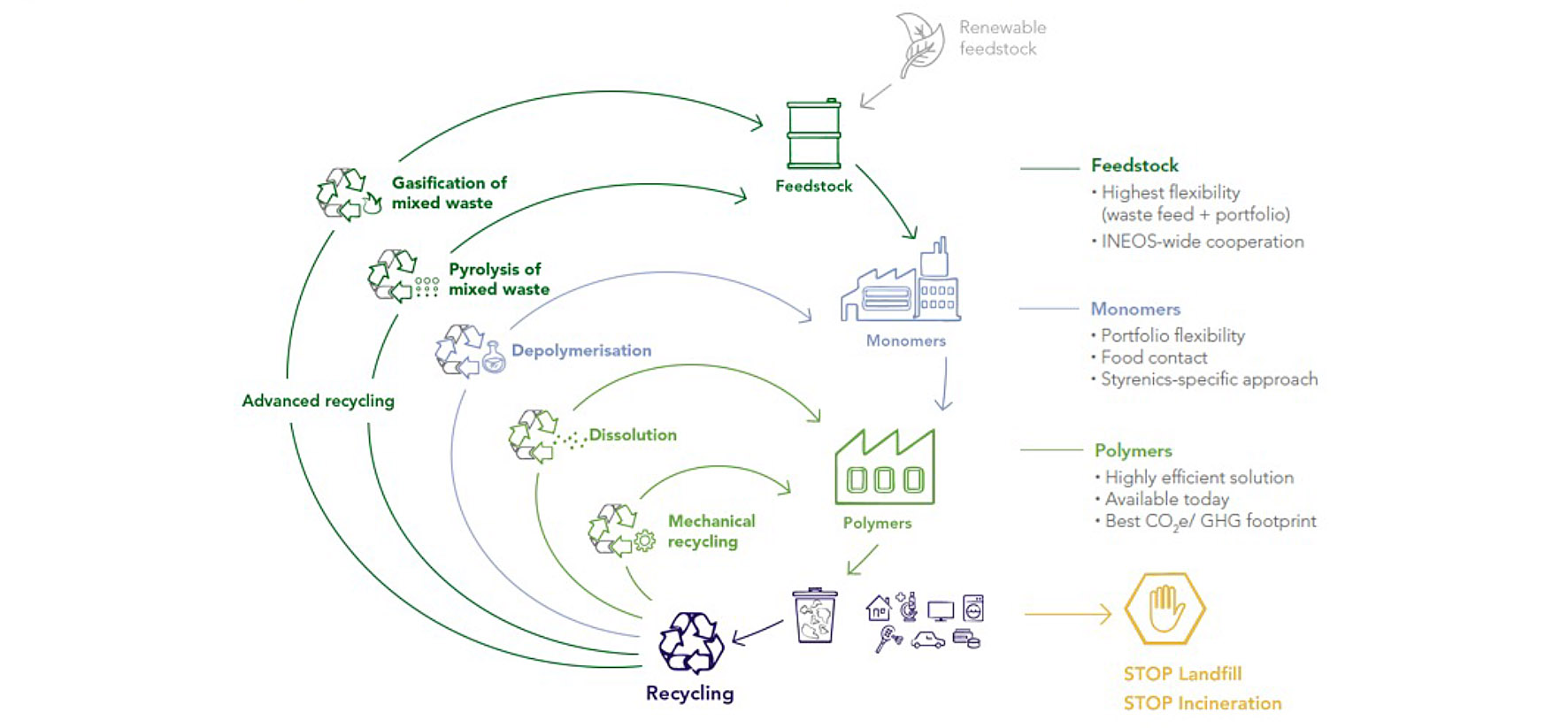
The traditional petrochemical value chain is very simple and linear: fossil fuels feedstock is converted into monomers, then to polymers; which is used to manufacture products for consumers and then disposed as waste. We want to stop waste going to landfills or being incinerated, and the proliferation of litter in general. We want to accelerate recycling. We have different technology options available, and we can cluster them into three different loops based on the entry point back into the value chain.
First, we have the polymer-to-polymer path with mechanical recycling and dissolution (solvent-based recycling). Then there is depolymerisation (polymer-to-monomer). This is a more styrenic-specific technology, because polystyrene has the unique ability to break down into its building block when it is exposed to heat in the right setting, bringing it to the monomer level. Then we have pyrolysis and gasification that uses mixed plastic waste that ends up at the feedstock level (polymer-to-feedstock).
At the polymer-to-feedstock stage, we are more flexible in terms of the waste that we can use and the products that we can manufacture from them. As we move to the polymer-to-polymer stage our CO2 footprint decreases further, so there is a trade-off between all of these technologies. Therefore, we need all these technologies because they are truly complementary to each other.
What else makes the recycling performance of styrenics unequalled?
First, there is a very low contamination uptake in the waste collection phase, keeping styrenics waste relatively clean. Styrenics are easily detectable and sortable from different polymers that match conventional quality levels, so can be steered into the optimum recycling processes easily, and have an excellent CO2 footprint.
Polystyrene is uniquely suited for food-contact to food-contact recycling. And it can undergo multiple mechanical recycling cycles while still retaining its property profile.
PRODUCT SAFETY UP. WORRIES DOWN.
Styrenics are safe. This fact applies to our conventional products as well as our ECO products. We will continue to ensure the performance quality and safety of our entire portfolio because we're putting huge efforts into proofing every new feedstock – be it recycled or renewable – extremely diligently. We're also investing in our capabilities and have taken significant steps to comply with all regulatory requirements.
COMMITMENT UP. OBSTACLES DOWN.
We have an ambitious programme. But we can’t achieve this all alone, there are some key enablers that need to be brought in place.
What do we require to make all of this happen?
Green energy is an important element of CO2 reduction. Fuel switches are an important and prompt enabler to bring carbon emissions down. But the plastics industry is not the only industry that has a demand for green energy. So, supply needs to go up to meet the rise in demand. Additionally, green power infrastructure must be developed. Otherwise, green power could become a bottleneck in a couple of years.
Today, a sufficient volume of waste is the bottleneck and a limiting factor for many of our recycling projects. We need expanded collection systems that are well regulated so that our industry has access to an adequate supply of waste to deliver products with recycled content.
There are different waste qualities available, and to allow for the high recycling rates we target – different recycling technologies need to be implemented. To ensure that we have a full suite of comprehensive recycling technologies available, we need full industry and regulatory acceptance of advanced recycling and mass balance to complement mechanical recycling.
As our industry continues to advance new circular and low carbon technology, we are confident that we will deliver on our commitment of “Performance up. Footprint down”. Our goals are ambitious, but we believe also achievable a million tonnes less CO2 emissions, 500,000 tonnes of sales of our ECO products, and 100% regulatory and safety compliance – and in the long term, we are committed to transforming to a net-zero business by 2050.