Meet a champion –
90 years old and counting
Styrenics polymers are an indispensable part of our lives today. They are the material of choice in a wide range of industries including automotive, healthcare, household, electronics, construction, packaging and toys/ sports/ leisure.
Most likely, your washing machine components are made with styrenics, your mobile phone contains styrenics, the steak you had for lunch today was protected by styrenics packaging, the yoghurt at breakfast was kept fresh in a cup made from styrenics, your car’s front grill and the dashboard may be made with styrenics… the list is endless…
Being lightweight and durable, styrenics help reduce the weight of cars resulting in reduced fuel use. It helps insulate our homes resulting in less energy consumption. It is a great choice for food packaging as it helps reduce the amount of food being wasted, keeping it fresher and safer.
Styrenics materials are used to make life-saving applications in the healthcare industry, a fact that became evident during the COVID-19 pandemic with detection kits, respiratory devices, safety goggles and face shields all benefiting from styrenics’ properties.
How an accidental invention
became a global bestseller
1839
Polystyrene was first discovered as
early as 1839 by German pharmacist
Eduard Simon by isolating a
substance from the bark of a styrax
tree that he called styrene (German:
Styrol). He noticed that the new
substance did not evaporate when
heated, but thickened into a jelly. He
called the new material styrene oxide
(German: Styroloxid), not knowing
he witnesses the first polymerisation
rather than an oxidation.
The rise of styrenics materials started
a century later, after Hermann
Staudinger had explained the
principle of polymerisation (Nobel
prize in 1953). First ideas for the
industrial production of polystyrene
were shared.
The road to the production of
polystyrene was paved in the years
1929 and 1930.
1929
In 1929, the production of styrene
monomer from ethylbenzene was
patented1 and one year later,
the continuous polymerisation of
styrene monomer to polystyrene was
described in yet another patent2. The
initial recipe was later perfected.
1931
In 1931, initial challenges were
overcome with the first ready-to-use
polystyrene – or: “Polystyrene II”,
as it was initially called – produced
by degassing volatile components
in vacuum3. Later enhancements of
the production process resulted in
improved material at a higher degree
of polymerisation: “Polystyrene III”
and “Polystyrene IV”.
1940's
The initial capacity of tens, and later
hundreds of tonnes per year grew
quickly and passed the 10,000 tonnes
per year mark in the 1940’s.
1 Deutsches Reichspatent DRP 550055 (August 9, 1929)
2 Deutsches Reichspatent DRP 634278 (October 2, 1930)
3 Deutsches Reichspatent DRP 644285 (August 15, 1931)
INEOS Styrolution:
the global leader in styrenics
In 1931, the global demand for polystyrene was served by a single production site Ludwigshafen, Germany. Today, 90 years later, INEOS Styrolution, the global leader in styrenics, continues to produce styrenics in Ludwigshafen while managing a range of sites producing polystyrene across all three global regions, EMEA, APAC and the Americas.
Polystyrene. Made for recycling.
Like no other.
Today, we are aware of styrenics polymers being part of the challenge we face with increased plastics waste and related pollution. At INEOS Styrolution, post-consumer waste is considered a valuable resource rather than waste. Together with a number of leading technology providers, INEOS Styrolution is addressing the challenge of moving towards a circular economy and recycling polystyrene, thus reducing plastic waste.
When exploring the recyclability of polystyrene, we were able to confirm that it is indeed made for recycling. It can be recycled via a range of technologies, thus allowing us to take the “single” out of “single use”.
As part of a pledge by the INEOS Group, INEOS Styrolution has committed to use, on average, 30% recycled content in products destined for polystyrene packaging in Europe, contribute to incorporating at least 325 k tonnes per year of recycled INEOS material into products and ensure 100% of polymer products can be recycled by 2025.
The future of Polystyrene
has already begun
In March this year, INEOS Styrolution brought mechanically recycled polystyrene to the market. Both recycled grades for General Purpose Polystyrene (GPPS) and High-Impact Polystyrene (HIPS) polystyrene are available in commercial volumes today.
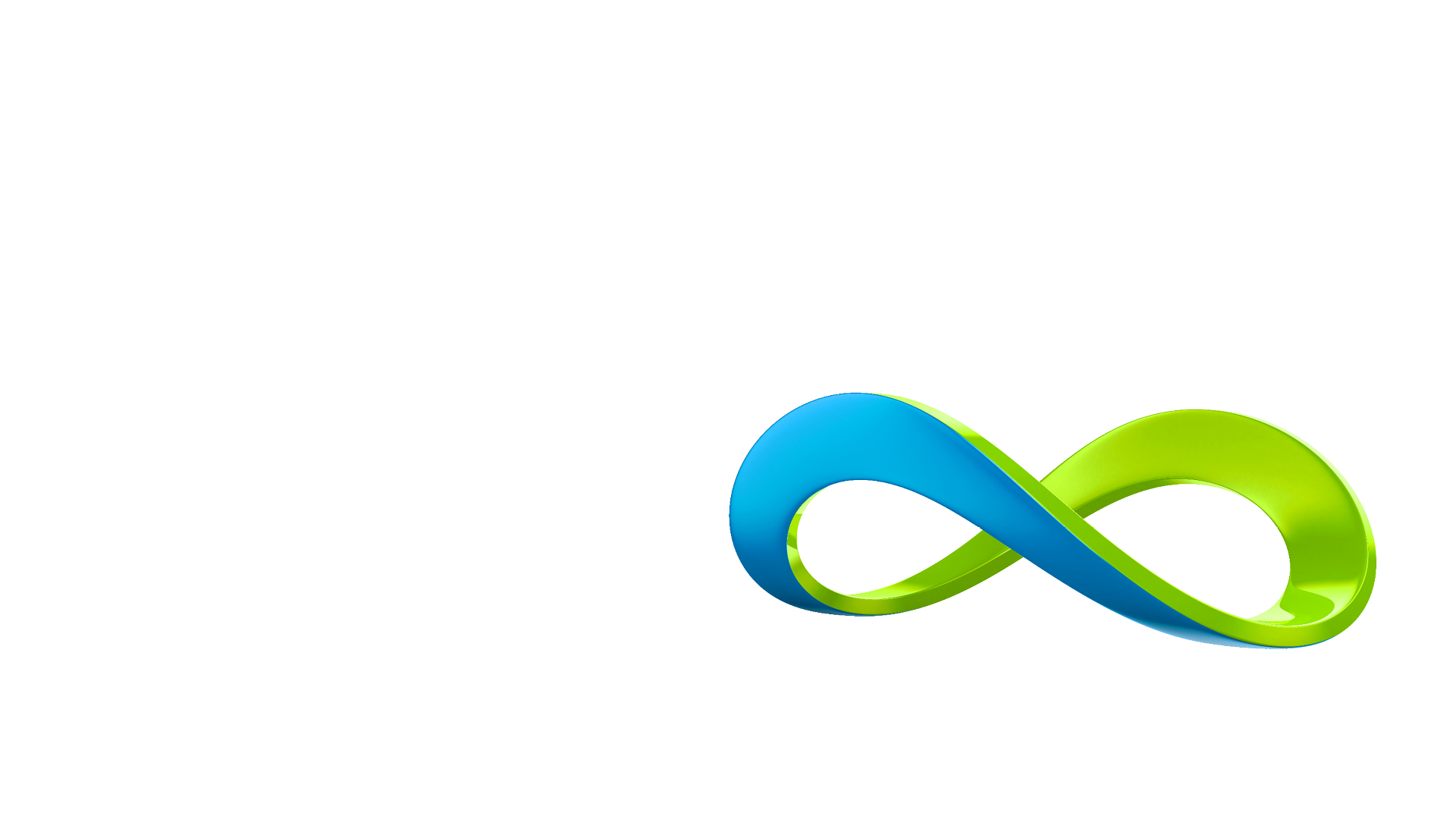
Driving circular solutions
for Polystyrene
According to latest developments, mechanically recycled polystyrene even promises to allow for food contact, bringing the material into a league of its own.
We also focus on advanced recycling methods for polystyrene. In 2019, INEOS Styrolution reported a breakthrough in advanced recycling of polystyrene with the first production of polystyrene from depolymerised material allowing for closing the loop towards a circular economy for polystyrene. This award-winning innovation takes advantage of the unique chemical property of polystyrene that allows reversing the polymerisation process.
INEOS Styrolution plays a leading role in driving the depolymerisation process forward. The company has built up a significant intellectual property related to the recycling of styrenics as documented in a range of fundamental patents.
In parallel, the company is addressing the challenge moving the technology from labscale to commercial scale resulting in a range of benefits from reducing waste to reducing the ecological footprint with less GHG emissions during the production process compared to producing virgin polystyrene from naphtha.
Together with technology partners, INEOS Styrolution plans the construction of depolymerisation plants in Wingles, France, in Channahon, the U.S. and collaborates with technology partners aiming at further recycling sites for polystyrene. We expect polystyrene recycled via depolymerisation to be available in 2023 at commercial scale.
Recycled polystyrene:
a lightweight material with a
lighter footprint
For almost a century, polystyrene has enhanced our lives and it is ready to serve us for centuries to come. It is made for recycling like no other, being one of the best sortable plastics in the waste stream and it shows very promising results in first life cycle assessments. First calculations predict a 50% lower carbon footprint than that of traditional virgin (fossil-based) styrene monomer production.
We are a global force in styrenics manufacturing determined to reshape our industry for the future. We strive to guarantee the benefits of styrenic products with a minimal environmental footprint.